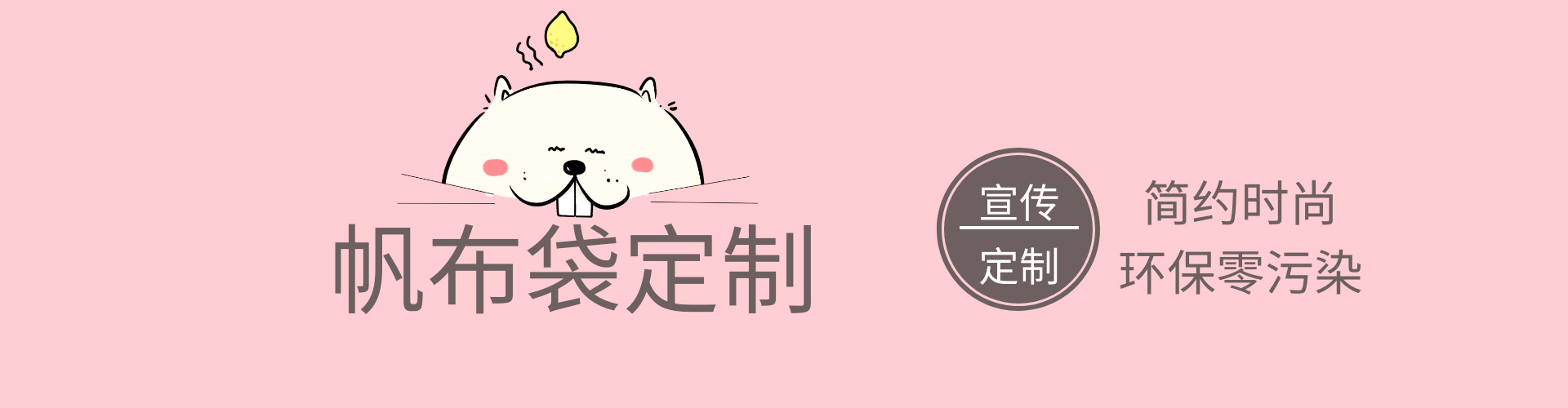
集團(tuán)動態(tài) News Information
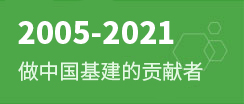
混凝土堵泵原因及對策
混凝土已成為用量最大的建筑材料,其質(zhì)量直接影響混凝土工程質(zhì)量。在混凝土生產(chǎn)、供應(yīng)過程中由于原材料波動、生產(chǎn)質(zhì)量控制不規(guī)范,施工過程亂加水等現(xiàn)象,常常出現(xiàn)一些質(zhì)量問題影響其質(zhì)量?;炷临|(zhì)量控制的根本在于過程控制,各個環(huán)節(jié)控制得當(dāng)是混凝土質(zhì)量的關(guān)鍵。結(jié)合生產(chǎn)過程中經(jīng)常出現(xiàn)的一些問題,如堵管問題,總結(jié)其形成原因和有效的預(yù)防措施,供大家參考,不當(dāng)之處歡迎大家留意指正。
堵管現(xiàn)象在混凝土泵送施工過程中時有發(fā)生,其對混凝土澆筑、施工及質(zhì)量具有重要的影響。在施工現(xiàn)場發(fā)現(xiàn),泵送混凝土堵管大多數(shù)由于坍落度損失過大,造成入泵前混凝土流動性差導(dǎo)致。其次,混凝土出機(jī)口坍落度大而擴(kuò)散度小,混凝土離析,和易性差導(dǎo)致堵管。所以減少混凝土坍落度損失和保證混凝土拌合物施工和易性(可泵性)是至關(guān)重要的。
泵送混凝土必須滿足輸送泵對拌合物的和易性要求,才能使混凝土拌合物在輸送管道中輸送暢通,不堵管。當(dāng)然也有設(shè)備的管道布置、操作不當(dāng),還有工地與混凝土公司溝通不當(dāng),壓車或者斷車等多種原因。堵管問題處理不當(dāng)會造成工程質(zhì)量和人、財、物的損失,從材料設(shè)備等角度全面分析才能做到降低或者避免堵管現(xiàn)象。
(一)造成混凝土堵管原因
(1)混凝土拌合物漿體不足,尤其時砂中小于0.315mm顆粒含量不足15%時,混凝土拌合物粘聚性差,不利于泵送。
(2)石子級配差,粒徑偏大,石子粒徑大于泵管的三分之一,長距離泵送時,石子粒徑大于泵管的四分之一,盡量減少超徑含量,一般不宜大于5%,防止泵送過程中骨料相互積壓,造成管道堵塞。砂子的細(xì)度模數(shù)要求在2.3~3.0之間,2區(qū)中砂,使用5mm~25mm連續(xù)顆粒級配的碎石,針片狀顆粒含量宜<8%。
(3)砂率選用不當(dāng),砂率過小,造成部分石子無砂漿包裹,或者砂率過大,漿體量包裹骨料表面厚度不足,混凝土拌合物無漿體,混凝土發(fā)散,粘聚性差。
(4)骨料吸水率大于2%,造成混凝土拌合物坍落度損失,黏度增加,泵送難度大造成堵管。砂、石含泥量高,造成對減水劑吸附量大,混凝土坍落度損失大,流動性差造成堵管。
(5)混凝土坍落度控制不當(dāng),坍落度過大造成漿石分離,泵送過程中漿體速度快于石子,造成骨料集中摩擦力增加而堵管,坍落度過小,混凝土拌合物流動性差造成堵管。
(6)管道布置不合理,管道接口處漏氣使管內(nèi)壓力降低造成堵管。
(7)泵管清洗不徹底,管道內(nèi)有硬化的混凝土,或者泵送混凝土前沒有使用砂漿潤管。
(8)泵送過程中出現(xiàn)斷車,間斷時間過程,管內(nèi)混凝土失去流動性,尤其是高溫夏季,長時間不能泵送。
(9)施工工程加水,片面追求大坍落度,造成混凝土離析,一旦出現(xiàn)泵送暫停,造成堵管。
(10)泵車操作人員操作不當(dāng)。
(11)混凝土運(yùn)輸時罐車因轉(zhuǎn)筒未轉(zhuǎn)動造成混凝土拌合物不均勻,骨料下沉,漿液上浮,在泵送時發(fā)生堵泵。
(二)預(yù)防堵管措施
(1)控制泵送混凝土漿體量,一般不宜低于280L/m3,泵送前使用砂漿或潤泵劑潤泵。
(2)嚴(yán)格控制石子粒徑和級配,國家現(xiàn)行有關(guān)標(biāo)準(zhǔn)規(guī)定,泵送高度在50m以下,最大粒徑與輸送管徑之比不宜大于1∶3;泵送高度在50~100m,最大粒徑與輸送管徑之比宜在1∶3~1∶4;泵送高度在100m以上,最大粒徑與輸送管徑之比宜在1∶4~1∶5。通常泵送高度在50m 以下的泵送混凝土的輸送管徑應(yīng)大于3倍的最大骨料粒徑,即泵送高度在50 m以下采用碎石的三級配泵送混凝土的管徑宜大于240mm??刂粕爸行∮?span>0.315mm細(xì)顆粒含量不低于15%,泵送中低強(qiáng)度等級混凝土?xí)r,砂細(xì)顆粒的含量控制20%左右。
(3)調(diào)整混凝土配合比,確?;炷涟韬衔餆o嚴(yán)重泌水、離析現(xiàn)象。泵送混凝土的坍落度一般控制在160~200mm范圍內(nèi),泵送高度和泵送水平距離對混凝土的坍落度造成的影響,一般泵送高度每提高30m,泵送距離每延長30m,混凝土的坍落度相應(yīng)提高20~30mm。
(4)布置管道時,盡量減少≤90°的彎管,進(jìn)行高層泵送時,水平管路的長度一般應(yīng)不小于垂直管路長度的15%,且應(yīng)在水平管路中接入管路截止閥,由水平轉(zhuǎn)垂直時的90°彎管,彎曲半徑應(yīng)大于500mm。
(5)泵送混凝土過程中,料斗內(nèi)應(yīng)保持一定數(shù)量的混凝土,不得吸空,并隨時監(jiān)控各種儀表和指示燈,出現(xiàn)不正常時,應(yīng)及時調(diào)整和處理?;炷凉?yīng)不及時時,應(yīng)每隔5~10分鐘泵送一次。若停止時間較長再泵送時,應(yīng)逆向運(yùn)轉(zhuǎn)一至二個行程,然后順向泵送。
(6)氣溫高時,注意覆蓋管道降溫。
(7)注意泵車保養(yǎng)、檢修。
(三)正確判定堵管部位
泵送混凝土堵管現(xiàn)象時有發(fā)生,發(fā)生堵管現(xiàn)象并不可怕,可怕的是在堵管發(fā)生后,不能及時準(zhǔn)確查找出堵管原因,排除堵管故障,耽誤解決堵管最佳時機(jī),使簡單正常的堵管變成嚴(yán)重堵管,甚至造成管道報廢,混凝土報廢,影響施工進(jìn)度。遇到堵管后,先進(jìn)行反泵疏通,疏通無效應(yīng)及時查找堵泵位置,清理疏通。堵管部位判定方法是:在泵機(jī)操作人員進(jìn)行正泵——反泵操作的同時,其他人員沿管路尋找堵塞部位。一般來說,從泵的出口起至堵塞部位會發(fā)生劇烈振動,而堵塞點(diǎn)以后的管路則是靜止的,堵塞部位有發(fā)悶的聲音和密實(shí)的感覺。一旦找到堵塞部位,在進(jìn)行正——反泵的同時,用木椎敲打該處,可能恢復(fù)暢通,無效應(yīng)立即拆卸該段管道進(jìn)行清洗。如堵塞部位判斷不準(zhǔn),也可進(jìn)行分段清洗。
(1)進(jìn)料口堵塞:液壓系統(tǒng)工作正常,泵送壓力較低,無異常聲音和振動,料斗料位不下降,出口有混凝土排除。
(2)分配閥出口堵塞:泵體發(fā)出振動,有異常噪聲,反泵時油壓表回到最高壓力,液壓系統(tǒng)突然中斷,混凝土返回不到料斗中。
(3)管道內(nèi)堵塞:油壓沖程次數(shù)增加,油壓升高,泵車同時振動,管道振幅較大,反泵時能吸出管道中部分混凝土,正泵時不能吸入料斗中的混凝土。
(4)堵塞點(diǎn)查找:用木錘敲擊管道,聲音沉悶處或管道內(nèi)有刺耳聲處,即是堵塞點(diǎn)。