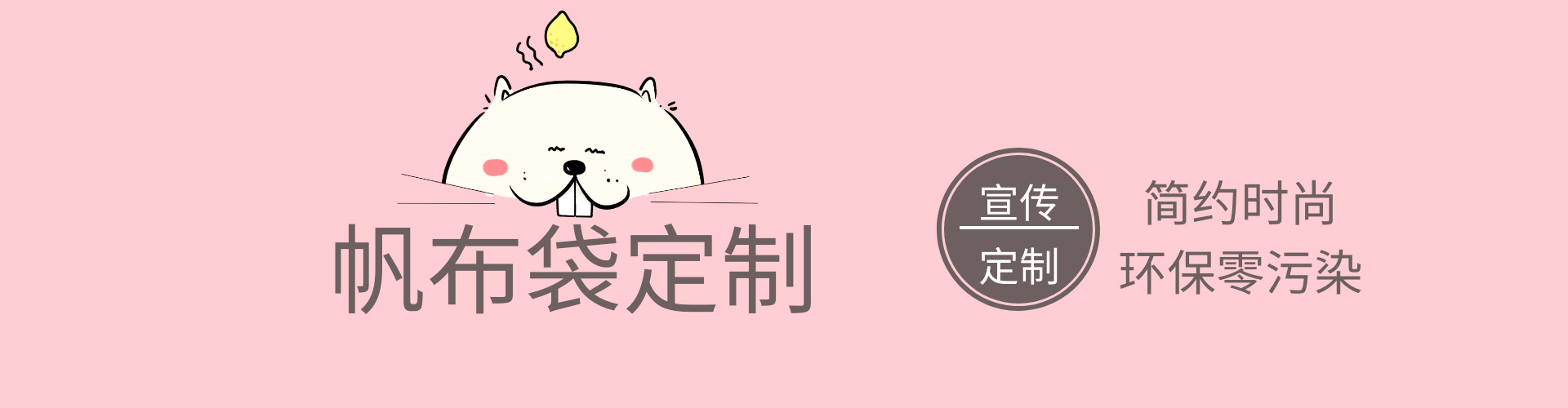
集團動態(tài) News Information
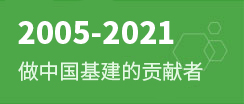
對半個世紀水泥質量發(fā)展道路的反思(三):水泥質量發(fā)展方向的修正
在回顧世界水泥質量發(fā)展道路的基礎上,已經(jīng)分析了水泥質量變遷與混凝土耐久性劣化的關系。庫馬爾·梅塔和理查德·W·伯羅斯[3]總結了近百年美國混凝土發(fā)展道路,他們提出與混凝土耐久性有關的水泥方面的問題,包括:①水泥用量增加了;②水泥強度特別是早期強度高了;③水泥C3S多了;④水泥比表面積增加了。
國內學者也有類似的意見。但對于如何解決這些問題,水泥和混凝土兩方面的意見很難統(tǒng)一。水泥方面似乎被禁錮于一種傳統(tǒng)的思維定勢之中,認為一百多年以來已經(jīng)建立并不斷完善的通用硅酸鹽水泥技術指標體系,其框架是無需置疑的,只需進行一些細節(jié)上的小的修補。
混凝土方面又較少考慮他們的意見對于水泥行業(yè)需要付出的一系列巨大代價,這些代價包括經(jīng)濟的、能源的和環(huán)境的。本文試圖根據(jù)混凝土耐久性的需要,探討對通用硅酸鹽水泥技術指標體系框架的修改。在滿足混凝土耐久性需要的同時,水泥行業(yè)如何以最小的經(jīng)濟、能源和環(huán)境代價,實現(xiàn)對水泥質量發(fā)展方向的修正。
1水泥質量發(fā)展方向存在的問題
最近的十余年間,來自于混凝土方面對水泥質量的批評已經(jīng)很多,提出了許多具體存在的問題。但很少有人指出,半個多世紀,甚至可以將時間追溯的更早一些,水泥質量的發(fā)展道路與混凝土耐久性的要求是背道而馳的。真正認識水泥質量發(fā)展方向的錯誤,并進行修正,才能保證混凝土結構的耐久性。
總結目前水泥質量存在的主要問題如下:
1)水泥強度特別是早期強度偏高;
2)水泥細度細;
3)熟料C3A含量偏高;
4)熟料C3S含量偏高;
5)水泥的堿含量偏高;
6)夏季出廠水泥溫度偏高。
上述問題導致:
1)水泥早期(水化后數(shù)分鐘至3d)化學減縮增加;
2)水泥早期水化熱增加;
3)水泥在數(shù)年及更長時間持續(xù)的強度增長能力減弱,甚至消失;
4)水泥開裂敏感性增加。
除前述水泥質量存在的主要問題之外,還存在以下的一般性問題:
1)僅以水泥的凝結時間、強度作為確定石膏摻量的依據(jù)。實際上水泥中石膏的摻量和形態(tài)與流變性能、開裂敏感性均密切相關。
2)水泥磨尾倉使用段做研磨體,導致水泥顆粒形貌變差。
3)使用料床粉磨作為水泥終粉磨,導致水泥顆粒形貌變差。
4)水泥標準對水泥與減水劑相容性未作規(guī)定,實際水泥于此參差不齊。
5)水泥標準沒有全面的水泥質量勻質性指標,水泥質量波動大,偶爾發(fā)生用戶非預期的、不可知的巨大變化。
將上述問題歸納總結,以混凝土耐久性破壞進行溯源,水泥質量存在的本質性(核心)問題有兩項:1)水泥早期水化速率過快;
2)水泥堿含量偏高(主要指三北地區(qū)而言)。
其余問題均可視為是這兩個本質問題的現(xiàn)象或原因。堿含量偏高固然是水泥早期水化速率、化學收縮過大的原因,但除此之外,堿會劣化水化產(chǎn)物形貌?;蛟S有人主張將化學減縮加大、水化熱增加也列入導致混凝土性能變差的本質原因?;瘜W減縮增加實際上是因為水泥早期水化速率加快,使水化產(chǎn)生的化學減縮在早期的測量結果增加了,并非真正的減縮增加。
真正能夠減小混凝土化學減縮的措施,只有降低水泥用量。水化熱的情況也與化學減縮近似,只是化學減縮在混凝土初凝之前是少害或無害的,水泥漿體硬化之后才會產(chǎn)生危害。水化熱在水泥漿體硬化之前和之后都是有害的,只有在混凝土達到最高內部溫升之后,水化熱的危害才會變小以致消失。因此,早期化學減縮、早期水化熱增加也可以視為水泥早期水化速率高的結果。
水泥行業(yè)普遍存在的一些不利于混凝土性能,特別是有害于混凝土耐久性的做法:
1)水泥強度等級越高(熟料含量越高),細度越細;
2)通過提高熟料C3A含量提高水泥早期強度或提高窯的臺時產(chǎn)量;
3)要求熟料鮑格公式計算的C3S含量大于一個很高的數(shù)值,例如60%;
4)水泥磨尾倉使用段做研磨體;
5)使用料床粉磨作為水泥終粉磨;
6)在水泥粉磨過程中加入以堿金屬鹽為主要成分的激發(fā)劑。
2混凝土若干技術要求辨析
半個多世紀水泥質量的變遷,堿含量的提高是由于水泥企業(yè)為了降低能耗、提高窯單位容積產(chǎn)量,主動采用窯外分解窯技術造成的。除此之外,C3S含量增加、早期強度提高以及細度變細都不是水泥企業(yè)的主動行為。水泥質量向錯誤方向的演變,是在水泥使用者不斷給水泥行業(yè)以誤導造成的。這種誤導有一些是技術性因素,也有一些是非技術性因素。例如水泥早期強度的不斷提高,是由于混凝土早期強度的要求,而混凝土早期強度提高又是業(yè)主、施工方的要求。在與建筑物有關的多方復雜關系中,總能看到利益、政績驅動的因素。今天,當水泥企業(yè)考慮修正水泥質量發(fā)展方向的時候,應該特別注意不能因為缺乏溝通與研究,再次受到水泥使用方的誤導。
毋庸置疑,半個多世紀以來混凝土耐久性劣化,很大一部分原因源于水泥強度特別是早期強度提高,細度變細。但如果混凝土行業(yè)要求水泥行業(yè)一定要降低水泥早期強度和細度,將可能再一次對水泥行業(yè)造成誤導。事實上導致混凝土耐久性劣化的是水泥的早期水化速率快,熟料的C3A、C3S含量高,水泥中熟料細顆粒多。
2.1水泥強度
理查德·W·伯羅斯在分析美國半個多世紀以來混凝土耐久性變差的原因時,特別強調水泥早期強度不斷提高的危害[6]。但降低水泥早期強度對于混凝土耐久性是充分條件而非必要條件。換言之,降低水泥早期強度對混凝土耐久性有利,但危害混凝土耐久性的本質,不是水泥的早期強度高,而是水泥的早期水化速率快。如果在提高水泥早期強度的同時,不加快水泥的早期水化速率,則對混凝土耐久性沒有明顯危害。
水泥早期水化速率高的原因包括:①熟料早期水化速率(強度)高;②水泥中含有較多的熟料細粉(<3μm);③水泥中石膏的形態(tài)和數(shù)量沒有得到正確的優(yōu)化;④堿含量高。將上述關系歸納如圖1所示。
圖1水泥早期強度影響因素分析
半個世紀以來,我們幾乎將水泥質量與水泥強度等同,同時又將水泥活性與水泥強度等同。認為提高水泥活性是提高水泥強度的唯一途徑。而忽視了水泥強度的物理作用,忽視了通過優(yōu)化水泥的粒度分布,提高水泥水化前的堆積密度,可以在顯著提高水泥強度的同時降低水化速率這一重要事實。
對于強度認識的誤區(qū)包括:
1)首先是水泥、混凝土的唯強度論:強度第一,甚至強度唯一。這一錯誤的觀念從混凝土傳遞到水泥行業(yè),多年來已經(jīng)深入人心,許多人認為不容置疑。
2)其次是水泥強度的唯化學論:把活性、化學反應能力與強度等同,認為強度的唯一來源是水泥(或混合材料)的化學反應能力。一個連帶的誤區(qū)是認為水泥高強必然高水化熱。
3)將按照標準方法檢驗(固定水灰比)的只具有相對意義的強度數(shù)值絕對化。事實上,強度是水灰比、齡期的函數(shù)。
唯強度論的出發(fā)點也許不錯,但結果卻令人沮喪。有人為了避免混凝土路面的損壞,將混凝土路面板的28d抗折強度提高到5MPa。隨著混凝土強度增加,其脆性也同時提高。
對因沖擊荷載而疲勞斷裂的水泥混凝土路面,高脆性將使其更加無法耐久。高強的同時必然是高脆性的、易開裂的混凝土,很難承受沖擊載荷。地震時的建筑物、混凝土路面、受到輪船撞擊的橋墩都是承受沖擊載荷。
1957建成的武漢長江大橋,半個多世紀以來歷經(jīng)了近80次撞擊,無結構性損壞。最嚴重的一次是一艘萬噸級油輪正面撞上了武漢長江大橋的7號橋墩。武漢長江大橋橋墩使用的是抗壓強度15~20MPa的混凝土。1988年建成的廣東九江大橋,2007年被一艘2000噸級的運砂船撞擊,發(fā)生160m垮塌。近年來橋梁混凝土的抗壓強度已經(jīng)提高30~50MPa,但被船撞垮橋梁的事故頻現(xiàn)。
唯化學論是又一個錯誤的思維定勢。水泥強度的唯化學論忽視了水泥石強度的本質。20世紀60年代,T.C.Powers基于對水泥石結構的假設及大量試驗結果,提出了反映水泥石強度與其孔隙率關系的膠空比公式:R=α0·Xn
式中:
R——水泥石強度;
α0——水泥凝膠的固有強度,即凝膠體在孔隙率為0時的強度;
n——試驗常數(shù),約為2.5~3;
X——膠空比,即水泥凝膠在水泥石中的填充程度,大小為凝膠體積與凝膠體積加毛細孔體積及氣孔體積之和的比值,主要與水灰比和水化程度有關。
水泥石孔隙率大小主要取決于水灰比。從水泥的水化硬化過程而言,決定水泥強度的因素可以分為化學作用和物理作用兩個方面。在水泥中含有較多熟料及高活性的混合材料,或熟料、混合材料的活性較高,都可以產(chǎn)生較多的水化產(chǎn)物,從而減小孔隙率,提高強度。
同時,如果提高水化前水泥顆粒的堆積密度,可以降低用水量,同樣可以降低水泥石的孔隙率,提高強度。利用物理作用提高水泥強度,特別是提高早期強度,可以使用較少的熟料,在大幅度提高強度的同時,降低水化熱。采用分別粉磨工藝,按照各自不同的要求分別控制熟料、混合材料的粒度分布,配制水泥時對粒度分布進行設計與控制,可以生產(chǎn)含有60%的熟料的水泥,3d抗壓強度高于熟料6MPa,28d抗壓強度高于熟料14MPa。同時水化熱降低。
日本水泥的粉磨工藝處于世界領先水平,分別粉磨技術在日本50年前就已經(jīng)開始應用,40年前已經(jīng)全部淘汰了混合粉磨工藝。筆者1999年在日本水泥廠看到的關于水泥強度的一個普遍現(xiàn)象是,與熟料強度比較,摻有15%混合材料的水泥,3d抗壓強度高于熟料5MPa,28d抗壓強度高于熟料10MPa。摻有50%混合材料的水泥,3d抗壓強度略低于熟料,28d抗壓強度略高于熟料。這已經(jīng)足夠滿足配制C60混凝土的需要。
不能將化學反應能力誤認為是強度的本質。強度的本質是孔隙率。所有能夠降低孔隙率的措施都可以提高強度。水泥的粒度分布經(jīng)過設計之后,強度可以提高到令我們吃驚的程度。即使是石灰石這樣的惰性物質,如果足夠細,也會有很高的強度貢獻,在水泥中等量替代熟料后,甚至會超過替代前的水泥強度。轉變思維模式,摒棄唯化學論,我們就可以生產(chǎn)出具有很高強度,同時水化熱很低的水泥。
2.2水泥細度
當希望與水泥性能建立聯(lián)系時,水泥細度的含義不夠明確,因為與水泥物理性能相關的是水泥粒度分布,篩余或比表面積只能作為水泥廠粉磨工藝一個控制指標。在混凝土行業(yè)很多人將細度與篩余等同。
與水泥早期強度類似,粗水泥也只是混凝土耐久性的充分條件而非必要條件?;炷烈笏嗖荒苓^細實際上想要表達的是:水泥過細會加快早期水化速率、提高早期水化熱、增加早期收縮、提高減水劑摻量、增加坍落度損失。
但事實上造成上述現(xiàn)象的主要是過細的熟料顆粒,混合材料(于混凝土則為摻和料)過細基本上不會導致上述問題。水泥中不同組分(熟料、石膏、混合材料)的水化行為不同,在水泥石微結構中的作用不同,對水泥性能的影響不同,粒度分布的要求也不同。
在探討水泥最佳粒度分布時必須分別考慮[9]。即分別研究熟料粒度分布、混合材料粒度分布和水泥粒度分布的要求。水泥中熟料的粒度分布要求是在保證較低細顆粒含量的前提下,盡量提高水化程度,熟料粒度分布應符合最佳性能RRSB方程?;旌喜牧狭6确植家笫?,與熟料配合后提高水泥顆粒的堆積密度使得熟料+混合材料組成的水泥的粒度分布符合Fuller曲線。
僅從水泥細度角度而言,符合現(xiàn)代混凝土要求的水泥應:①單方混凝土中盡量低的熟料含量;②早期(數(shù)分鐘至3d)盡量低的水化速率;③28d之內足夠的水化程度,且保持5~10年持續(xù)提供水化產(chǎn)物的能力;④粉體顆粒具有較高的堆積密度。目前我國廣泛應用的采用混合粉磨工藝的水泥,不符合上述要求。為滿足上述要求,熟料的細粉(<3μm顆粒)要有一個較低的限量,筆者建議一般性的標準 <10%,嚴格標準<8%,同時混合材料更多地含有細粉。這需要采用分別粉磨工藝。
2.3需水量
在水泥和混凝土行業(yè)都有“需水量”這一簡稱,但其含義不同。在混凝土行業(yè)需水量指單方混凝土用水量,在水泥行業(yè)需水量指水泥標準稠度用水量。
水泥標準稠度用水量包括4個部分:①固體顆粒表面的吸附水(包括顆粒之間空隙的水);②水泥初始水化消耗的水;③稀釋水泥初始水化產(chǎn)物的水;④火山灰質等具有開口孔和內比表面積的材料吸附到材料內部的水。混凝土用水量的組成與水泥標準稠度用水量大致相同,多出了砂石表面吸附水,但各部分的比例不同。
混凝土單方用水量并不是水泥標準稠度用水量的單值函數(shù),其影響因素包括:①水泥的標準稠度用水量;②水泥與減水劑相容性;③減水劑的質量和用量;④粉煤灰的含碳量;⑤砂石材料的含泥量;⑥混凝土所有膠凝材料的粒度分布。對于今天已經(jīng)普遍使用減水劑的流態(tài)混凝土,水泥標準稠度用水量與單方混凝土用水量不能簡單對應的原因還在于,檢驗水泥標準稠度用水量時沒有減水劑的存在,而拌和混凝土時使用了減水劑。
使用減水劑后固體顆粒(主要是粉體顆粒)表面的吸附水(包括填充顆粒之間空隙的水)明顯減少。有一個能夠說明問題的例證:向水泥中摻入20%的很細的礦渣粉,例如比表面積600m2/kg,水泥的標準稠度用水量是增加的。用這種水泥拌和的混凝土用水量卻是減少的。對這一現(xiàn)象混凝土行業(yè)稱為礦物減水效應。
3對水泥質量發(fā)展方向的修正
前文[1-2]及本文已經(jīng)盡量充分討論了當今混凝土耐久性變差與水泥質量的密切關系。今后我們能否沿著過去幾十年水泥質量的方向繼續(xù)前行?答案顯然是否定的,混凝土耐久性不允許。能否轉身向后,重新回到幾十年前?答案同樣也是否定的,巨大能源和環(huán)境的壓力使然。我們應該尋找一條更好的途徑,以較小的能源、資源、環(huán)境和經(jīng)濟代價達到既定目標——生產(chǎn)可以使混凝土耐久的水泥。以下筆者試圖對此進行探討。
討論水泥質量發(fā)展方向的修正,或水泥質量的改善,是基于這樣的認識:①半個世紀以來,中國與世界其他發(fā)達國家一樣,水泥質量是在沿著一條錯誤的方向發(fā)展;②通用水泥標準體系的框架必須進行根本性的修改。在研討修正水泥質量發(fā)展方向的時候筆者特別強調范式轉換。
3.1難以改變的對混凝土耐久性不利影響因素
主要是熟料C3S活性、堿含量,盡管它們影響顯著,但難以改變。
3.1.1 熟料C3S活性
水泥早期水化速率高的原因已如圖1所示。其中熟料C3S數(shù)量和活性的增加是半個多世紀以來水泥質量方面最大的變化。20世紀70年代窯外分解窯和與之配套的高效篦冷機開始應用,顯著提高了熟料的煅燒強度,熟料高C3S含量成為可能。不僅熟料中鮑格公式法計算的C3S含量可以高達60%以上,而且,窯外分解窯普遍采用快燒急冷的工藝方式,一方面使得熟料中實際存在的C3S可以比鮑格公式計算值高8%~10%(絕對值);另一方面,熟料中的硅酸鹽礦物晶格缺陷顯著增加,使得熟料水化反應速率增加。這些都使熟料早期水化速率顯著加快。由于我國一直采用混合粉磨工藝,水泥中熟料細粉的含量隨著水泥細度變細而增加。這又使得水泥早期水化速率增加。熟料C3S數(shù)量可以通過降低KH調整,但其活性卻很難降低,或者說降低C3S活性需要付出很高經(jīng)濟、能源和環(huán)境代價。
3.1.2 熟料堿含量
熟料堿含量是伴隨預熱器窯和窯外分解窯的普及和窯系統(tǒng)粉塵排放量減少而提高的,原因在于預熱器窯和窯外分解窯在窯內高溫區(qū)進入氣相的堿,無法像其他窯型那樣在窯外冷凝到粉塵表面排除到窯外,所有原燃材料帶入的堿幾乎全部留在熟料中。除非在水泥廠附近找到低堿的替代原料,否則能有效降低熟料堿含量的措施只有旁路放風,但這會顯著增加熱耗。對于新建水泥廠可以慎重選擇廠址,避免使用高堿原料。
3.2對水泥質量發(fā)展方向的修正
既然已經(jīng)明確水泥存在的本質性問題是早期水化速率快、堿含量高,那么對水泥質量修正的方向也就明確了。降低堿含量的困難已如前述。如果不能以較低的代價降低堿含量,要解決的核心問題就是降低水泥早期水化速率。技術路線如圖2所示。粗線部分為重點內容。
圖2 降低水泥早期水化速率技術路線
對于圖2給出的技術路線,可以概括表述為:使用低C3A、C3S的熟料,采用分別粉磨工藝,生產(chǎn)早期水化速率低,而強度并不太低的水泥。
3.3優(yōu)質水泥的基本特征
早年筆者曾經(jīng)提出若干從保證混凝土性能特別是混凝土耐久性考慮的,優(yōu)質水泥的基本特征:
1)單方混凝土的熟料用量較少;
2)較低的早期水化速率和水化熱;
3)與高效減水劑具有良好的相容性;
4)全面的水泥質量勻質性指標;
5)合理的早期、后期強度和至少保持10年內持續(xù)的強度增長;
6)粒度分布合理,顆粒球形指數(shù)高,堆積密度高;
7)較小的體積收縮;
8)適宜的堿含量;
9)夏季較低的出廠水泥溫度。
3.4提高混凝土耐久性水泥生產(chǎn)的技術措施
為提高混凝土耐久性,水泥生產(chǎn)可以采取的主要技術措施包括:
1)改變熟料礦物組成:C3A<5%,C3S<50%。
2)盡量降低熟料中的堿含量,同時控制硫堿比不低于0.8。
3)水泥粉磨采用分別粉磨。熟料+石膏的終粉磨采用球磨機+高效選粉機(選粉效率90%以上),以期得到形貌良好、粒度分布集中的熟料粉。熟料粉RRSB均勻性系數(shù)達到1.35以上。
4)混合材料粉磨優(yōu)先選擇立磨,并粉磨至多種細度分別儲存,惰性材料(如石灰石)最細。
5)對水泥的粒度分布進行設計、控制,使得熟料粉+多種混合材料粉組成的水泥的粒度分布符合Fuller曲線。
6)以水泥的早期水化速率、流變性能和開裂敏感性作為確定水泥中石膏種類、摻量的優(yōu)先依據(jù)。
7)出磨水泥經(jīng)過至少3d庫存后出廠。
8)夏季降低出廠水泥溫度至80℃以下。
3.5 對通用硅酸鹽水泥標準進行根本性修訂
盡管我們時常以水泥標準是最低質量要求為理由,拒絕對水泥標準的修改,但水泥標準對水泥質量巨大的引導作用使得我們欲改變水泥質量,必須先改變水泥標準。對此筆者建議:
1) 建立低水灰比(在0.38~0.40之間選取固定值)強度檢驗方法,廢止現(xiàn)行ISO強度檢驗方法(出口水泥可以保留);
2)增加熟料鮑格公式計算C3A、C3S的上限指標;
3)增加熟料硫堿比下限指標;
4)增加水泥早期水化速率上限指標;
5)增加水泥1d、3d水化熱上限指標;
6)增加水泥堿含量上限指標;
7)增加對水泥開裂敏感性的限制;
8)增加水泥與減水劑相容性下限指標;
9)增加3d/28d強度比值的上限指標,增加水泥強度28d/365d強度比值的上限指標;
10)增加水泥與減水劑相容性、強度、凝結時間、細度的標準偏差上限指標;
11)水泥初凝時間下限指標變?yōu)?20min;
12)適當調整目前通用硅酸鹽水泥的其他指標。
4結束語
1)半個多世紀以來混凝土耐久性越來越差,水泥質量錯誤的發(fā)展方向是最重要的原因。水泥質量發(fā)展方向與混凝土耐久性相悖的主要原因,來自反科學的利益驅動和認識的局限。如不能盡快徹底改變水泥質量的發(fā)展方向和現(xiàn)狀,混凝土耐久性問題就無法從根本上改觀,我國每年數(shù)千億的混凝土建筑物,幾十年之后面臨的維修和重建費用,數(shù)目之大讓人不寒而栗。美國目前每年混凝土建筑物的維修費用高達數(shù)千億美元。
2)混凝土耐久性不斷劣化的事實,讓我們不得不對水泥質量發(fā)展方向產(chǎn)生懷疑,欲扭轉水泥質量發(fā)展方向,則必須從根本上轉變水泥質量的唯強度論、唯化學論等一系列錯誤觀念,從根本上修訂現(xiàn)有通用硅酸鹽水泥標準的框架。
3)將水泥質量作為一個重要的變量,突破現(xiàn)有通用硅酸鹽水泥質量標準,研究水泥質量與混凝土耐久性關系。在此基礎上重新建立通用硅酸鹽水泥質量標準體系。
4)幾十年來我國水泥標準一直不斷追隨西方發(fā)達國家,今天,當他們已經(jīng)走向錯誤方向的時候,我們應該有勇氣走自己的路。